Understanding Welding WPS Requirements: Finest Practices and Techniques for Quality Welds
In the world of welding, understanding Welding Procedure Requirements (WPS) standards is an essential component that directly affects the quality and stability of welds. As we browse through the intricacies of welding WPS criteria, uncovering key insights and methods for achieving top-tier welds will be extremely important for welders seeking to stand out in their craft and create welds that stand the examination of time.
Comprehending Welding WPS Specifications

Inspectors depend on WPS paperwork to validate that welding treatments are being complied with appropriately and that the resulting welds are of high quality. Designers make use of WPS requirements to make welding procedures that make sure the resilience and integrity of welded structures.
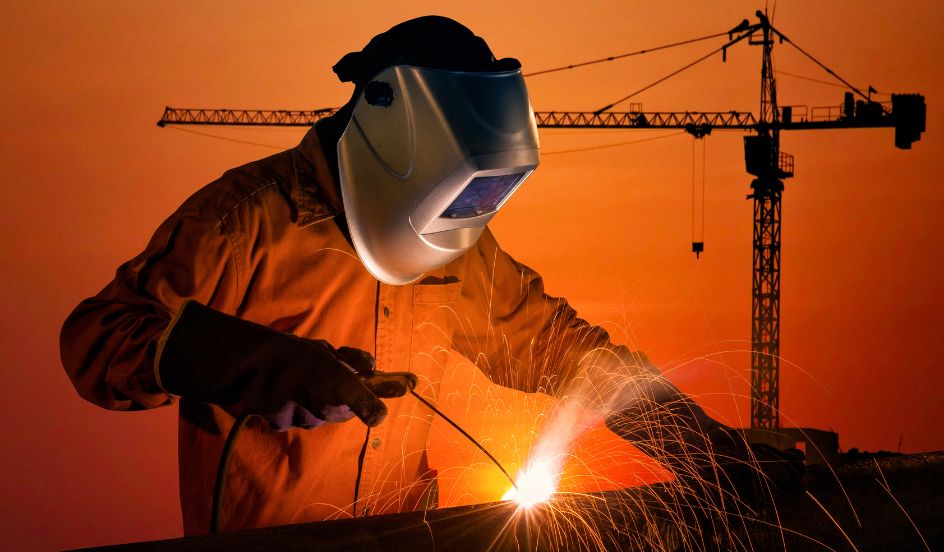

Crucial Devices for Top Quality Welds
Understanding welding WPS requirements is crucial for welders to efficiently utilize the crucial tools needed for producing top quality welds. The type of welding equipment needed depends on the welding procedure being used, such as MIG, TIG, or stick welding. Cable brushes and chipping hammers are necessary for cleaning the weld joint before and after welding to get rid of any type of contaminations that could impact the quality of the weld.
Secret Strategies for Welding Success
To attain welding success, one have to master the essential strategies crucial for creating top quality welds. One vital technique is preserving the proper arc length. Keeping the electrode at the optimal distance from the workpiece is important for producing strong, uniform welds. Additionally, managing the traveling rate is extremely important. Relocating too quickly can result in inadequate penetration, while relocating too slowly can result in too much warmth input and potential problems. Appropriate adjustment of the electrode angle is an additional vital technique. The angle at which the electrode is held can impact the grain form and infiltration of the weld. more info here In addition, guaranteeing constant gun angle and direction of travel is necessary for harmony in the weld grain. Last but not least, maintaining a stable hand and a stable welding setting throughout the process is crucial to accomplishing precision and consistency in the welds. By mastering these key strategies, welders can boost the high quality of their job and attain welding success.
Ensuring Conformity With WPS Criteria
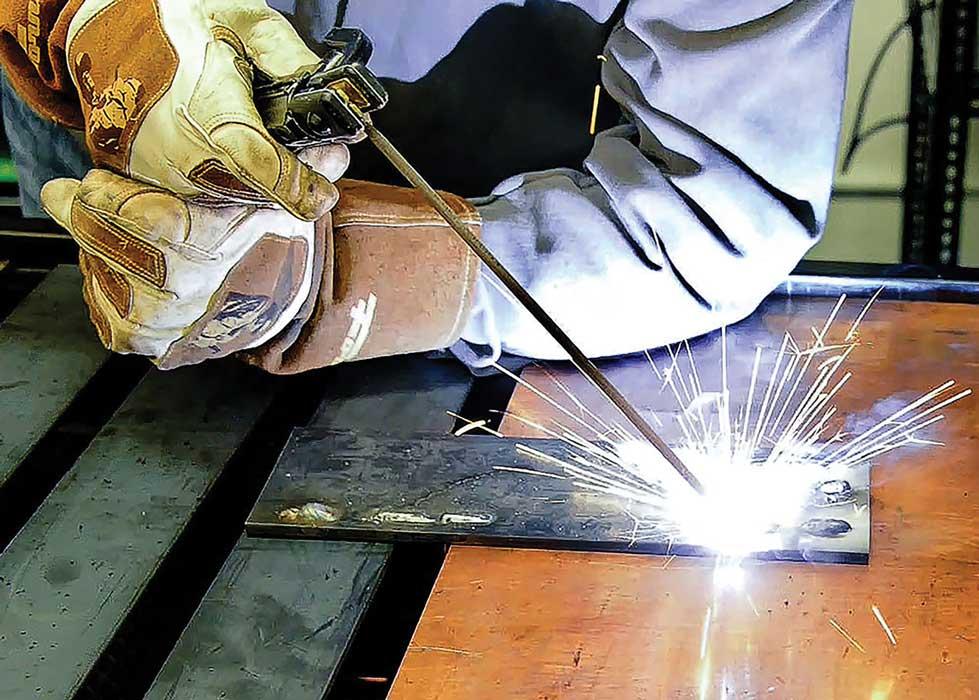
In addition, welders should undergo training to familiarize themselves with the WPS standards appropriate to their work. Regular audits and examinations should be conducted to verify that welding activities align with the recommended WPS guidelines. Additionally, maintaining comprehensive records of welding parameters, equipment calibration, and evaluation results is essential for demonstrating compliance with WPS standards - welding WPS. By diligently sticking to WPS criteria, welders can make certain that their job satisfies the necessary high quality levels and contributes to the total success of the welding task.
Troubleshooting Common Welding Issues
When faced with common welding concerns, determining the root cause is critical for reliable troubleshooting. One common trouble is the existence of find more porosity in welds, usually triggered by contaminants such as rust, oil, or wetness. To resolve this, ensuring correct cleaning of the base steel before welding and making use of the right shielding gas can substantially decrease porosity. An additional issue regularly experienced is absence of fusion, where the weld falls short to correctly bond with the base material. This can stem from poor heat input or inappropriate welding technique. Changing parameters such as voltage, cable feed rate, or travel speed can aid enhance blend. Furthermore, distortion, fracturing, and spatter are common welding obstacles that can be mitigated with correct joint preparation, constant warmth control, and selecting the proper welding consumables. By extensively understanding these typical welding concerns and their root triggers, welders can properly troubleshoot issues and attain top quality welds.
Verdict
In conclusion, mastering welding WPS standards requires an extensive understanding of the standards, using necessary devices, and applying vital strategies for effective welds. Making sure compliance with WPS standards is essential for creating high quality welds and avoiding usual welding concerns. By adhering to ideal methods and practices, welders can achieve dependable and constant lead to their welding projects.
In the world of welding, understanding Welding Procedure Spec (WPS) standards is a critical part that straight influences the quality and honesty of welds.When diving into the realm of welding techniques, a vital element to comprehend is the importance and intricacies of Welding Treatment Spec (WPS) click to read more standards. WPS criteria supply an in-depth standard for welding procedures, guaranteeing consistency, top quality, and security in the welding procedure. The kind of welding machine required depends on the welding process being used, such as MIG, TIG, or stick welding.Accomplishing welding success through the proficiency of essential strategies requires a comprehensive understanding and adherence to Welding Treatment Spec (WPS) standards.